The DeWALT DW735 Manual is your essential resource for harnessing the full potential of your 12-1/2" Heavy Duty Portable Thickness Planer. This comprehensive manual provides detailed setup instructions, operational guidance, and crucial safety tips to ensure efficient and safe planing. Whether you are a professional woodworker or a DIY enthusiast, the DeWALT DW735 Manual equips you with all the necessary knowledge to maintain your tool’s optimal performance.
DeWALT DW735 Heavy-Duty Portable Thickness Planer Instruction Manual
Definitions: Safety Alert Symbols and Words
This instruction manual uses the following safety alert symbols and words to alert you to hazardous situations and your risk of personal injury or property damage.
- DANGER: Indicates an imminently hazardous situation which, if not avoided, will result in death or serious injury.
- WARNING: Indicates a potentially hazardous situation which, if not avoided, could result in death or serious injury.
- CAUTION: Indicates a potentially hazardous situation which, if not avoided, may result in minor or moderate injury.
- NOTICE: Indicates a practice not related to personal injury which, if not avoided, may result in property damage.
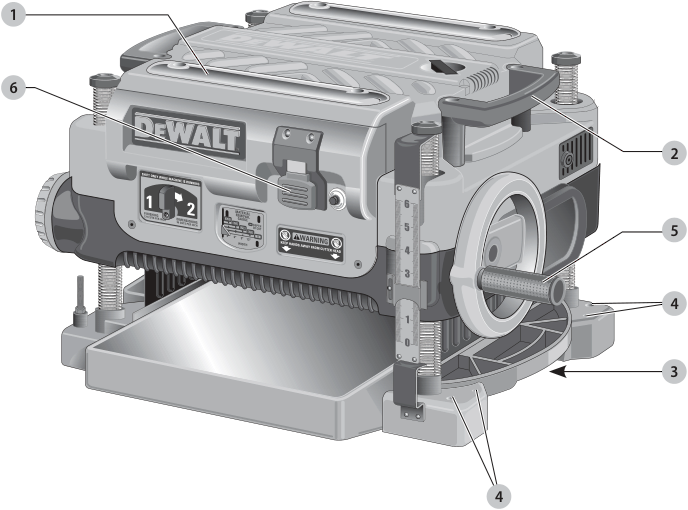
- Planer
- Side carrying handles
- Base handles
- Bench mounting holes
- Crank handle
- On/off switch
If you have any questions or comments about this or any DeWALT tool, call us toll free at: 1-800-4-DeWALT (1-800-433-9258).
General Power Tool Safety Warnings
SAVE ALL WARNINGS AND INSTRUCTIONS FOR FUTURE REFERENCE
The term "power tool" in the warnings refers to your mains-operated (corded) power tool.
General Safety Instructions
- KEEP GUARDS IN PLACE and in working order.
- REMOVE ADJUSTING KEYS AND WRENCHES . Form a habit of checking to see that keys and adjusting wrenches are removed from tool before turning it on.
- KEEP WORK AREA CLEAN . Cluttered areas and benches invite injuries.
- DON'T USE IN DANGEROUS ENVIRONMENT. Don't use power tools in damp or wet locations, or expose them to rain. Keep work area well-lighted. Always operate tool in a well-ventilated area free of combustible materials, gasoline or solvent vapors. If sparks come in contact with flammable vapors, they may ignite, causing fire or explosion.
- KEEP CHILDREN AWAY. All visitors should be kept safe distance from work area.
- MAKE WORKSHOP KID PROOF with padlocks, master switches, or by removing starter keys.
- DON'T FORCE TOOL. It will do the job better and safer at the rate for which it was designed.
- USE RIGHT TOOL. Don't force tool or attachment to do a job for which it was not designed.
- USE PROPER EXTENSION CORD. Make sure your extension cord is in good condition. When using an extension cord, be sure to use one heavy enough to carry the current your product will draw. An undersized cord will cause a drop in line voltage resulting in overheating and loss of power. The Minimum Gauge for Cord Sets table shows the correct size to use depending on cord length and nameplate amperage rating. If in doubt, use the next heavier gauge. The smaller the gauge number, the heavier the cord. When operating a power tool outside, use an outdoor extension cord marked "W-A" or "W". These cords are rated for outdoor use and reduce the risk of electric shock.
- WEAR PROPER APPAREL. Do not wear loose clothing, gloves, neckties, rings, bracelets, or other jewelry which may get caught in moving parts. Non-slip footwear is recommended. Wear protective hair covering to contain long hair. Air vents often cover moving parts and should also be avoided.
- ALWAYS USE SAFETY GLASSES. Also use face or dust mask if cutting operation is dusty. Everyday eyeglasses only have impact-resistant lenses, they are not safety glasses.
- SECURE WORK. Use of clamps or a vise to hold work when practical. It’s safer than using your hands and it frees both hands to operate tool.
- DON'T OVERREACH. Keep proper footing and balance at all times.
- MAINTAIN TOOLS WITH CARE. Keep tools sharp and clean for best and safest performance. Follow instructions for lubricating and changing accessories.
- DISCONNECT TOOLS before servicing; when changing accessories, such as blades, bits, cutters, and the like.
- REDUCE THE RISK OF UNINTENTIONAL STARTING. Make sure switch is in off position before plugging in.
- USE RECOMMENDED ACCESSORIES. Consult the instruction manual for recommended accessories. The use of improper accessories may cause the risk of injury to persons.
- NEVER STAND ON TOOL. Serious injury could occur if the tool is tipped or if the cutting tool is unintentionally contacted.
- CHECK DAMAGED PARTS. Before further use of the tool, a guard or other part that is damaged should be carefully checked to determine that it will operate properly and perform its intended function—check for alignment of moving parts, binding of moving parts, breakage of parts, mounting, and any other conditions that may affect its operation. A guard or other part that is damaged should be properly repaired or replaced.
- DIRECTION OF FEED. Feed work into planer according to the direction of feed arrows on top of the unit.
- NEVER LEAVE TOOL RUNNING UNATTENDED. TURN POWER OFF. Don’t leave tool until it comes to a complete stop.
Safety Rules for Surface Planers
- Do not operate this machine until it is completely assembled and installed according to the instructions. A machine incorrectly assembled can cause serious injury.
- Obtain advice from your supervisor, instructor, or another qualified person if you are not thoroughly familiar with the operation of this machine. Knowledge is safety.
- Follow all wiring codes and recommended electrical connections to prevent shock or electrocution.
- Keep knives sharp and free from rust and pitch. Dull or rusted knives work harder and can cause kickback.
- Never turn the machine "ON" before clearing the table of all objects (tools, scraps of wood, etc.). Flying debris can cause serious injury.
- Never turn the machine "ON" with the workpiece contacting the cutterhead. Kickback can occur.
- Secure the machine to a supporting surface to prevent the machine from sliding, walking or tipping over.
- Besurethatthecutterknivesaremountedas described in the instruction manual and check that all bolts are firmly tightened before connecting unit to power source.
- Avoid awkward operations and hand positions. A sudden slip could cause a hand to move into the knives.
- Keep arms, hands, and fingers away from the cutterhead, the chip exhaust opening, and the feed rollers to prevent severe cuts.
- Never reach into the cutterhead area while the machine is running. Your hands can be drawn into the knives.
- Do not stand in line with the workpiece. Kickback can cause injury.
- Allow the cutterhead to reach full speed before feeding a workpiece. Changing speeds while planing can cause kickback.
- When planing bowed stock, place the concave (cup down) side of the stock on the table and cut with the grain to prevent kickback.
- Do not feed a workpiece that is warped, contains knots, or is embedded with foreign objects (nails, staples, etc.). Kickback can occur.
- Do not feed a short, thin, or narrow workpiece into the machine. Your hands can be drawn into the knives and/or the workpiece can be thrown at high speeds. See the Operation section of this instruction manual for details.
- Do not feed a workpiece into the outfeed end of the machine. The workpiece will be thrown out of the opposite side at high speeds.
- Remove shavings only with the power "OFF" and the cutterhead stopped to prevent serious injury.
- Properly support long or wide work pieces. Loss of control of the workpiece can cause serious injury.
- Never perform layout, assembly or set-up work on the table/work area when the machine is running. Serious injury will result.
- Turn the machine "OFF", disconnect it from the power source, and clean the table/work area before leaving the machine. Lock the switch in the "OFF" position to prevent unauthorized use. Someone else might accidentally start the machine and cause injury to themselves or others.
- Additional information regarding the safe and proper operation of power tools (i.e. a safety video) is available from the Power Tool Institute, 1300 Sumner Avenue, Cleveland, OH 44115-2851 ( www.powertoolinstitute.com ). Information is also available from the National Safety Council, 1121 Spring Lake Drive, Itasca, IL 60143-3201. Please refer to the American National Standards Institute ANSI 01.1 Safety Requirements for Woodworking Machines and the U.S. Department of Labor Regulations.
Supplemental Safety Rules for Planers
- To avoid injury, never rotate the cutterhead directly with your hands.
- Keep hands away from the underside of the cutterhead carriage.
- Never clear clogs, make cutter knife replacement, or any other repairs/adjustments with unit plugged in.
- Make certain that the switch is in the "OFF" position before connecting plug to a power source.
- Stay alert — never operate the unit when tired or under the influence of drugs, alcohol, or medication.
- Do not use in dangerous environments. Do not use near flammable substances, in damp or wet locations, or expose to rain.
- Never plane material which is shorter than 12" (304.8 mm), narrower than 3/4" (19.05 mm), or wider than 12" (304.8 mm) or thinner than 1/2" (12.7 mm).
- Exhaust chute: remove shavings with brush or vacuum after power has been shut off and cutterhead has stopped rotating.
- Always locate planer with proper clearance on the outfeed side of the unit to prevent pinching or binding of the workpiece against any obstacle.
- Maintain the proper relationships of infeed and outfeed table surfaces and cutterhead knife path.
- Lock the speed setting securely before feeding the workpiece through the machine. Changing speeds while planing can cause kickback.
Additional Safety Information
ALWAYS WEAR CERTIFIED SAFETY EQUIPMENT:
- ANSI Z87.1 eye protection (CAN/CSA Z94.3).
- ANSI S12.6 (S3.19) hearing protection.
- NIOSH/OSHA/MSHA respiratory protection.
- lead from lead-based paints,
- crystalline silica from bricks and cement and other masonry products, and
- arsenic and chromium from chemically-treated lumber.
Your risk from these exposures varies, depending on how often you do this type of work. To reduce your exposure to these chemicals: work in a well-ventilated area, and work with approved safety equipment, such as those dust masks that are specially designed to filter out microscopic particles.
Avoid prolonged contact with dust from power sanding, sawing, grinding, drilling, and other construction activities. Wear protective clothing and wash exposed areas with soap and water. Allowing dust to get into your mouth, eyes, or lay on the skin may promote absorption of harmful chemicals.
Power Connections
A separate electrical circuit should be used for your machines. This circuit should not be less than #12 wire and should be protected with a 20 Amp time lag fuse.
Motor Specifications
Your machine is wired for 120 Volts, 60 HZ alternating current. Before connecting the machine to the power source, make sure the switch is in the "OFF" position.
Grounding Instructions
- All grounded, cord-connected machines:
- In the event of a malfunction or breakdown, grounding provides a path of least resistance for electric current to reduce the risk of electric shock. This machine is equipped with an electric cord having an equipment-grounding conductor and a grounding plug. The plug must be plugged into a matching outlet that is properly installed and grounded in accordance with all local codes and ordinances.
- Do not modify the plug provided - if it will not fit the outlet, have the proper outlet installed by a qualified electrician.
- Improper connection of the equipment-grounding conductor can result in risk of electric shock. The conductor with insulation having an outer surface that is green with or without yellow stripes is the equipment-grounding conductor. If repair or replacement of the electric cord or plug is necessary, do not connect the equipment-grounding conductor to a live terminal.
- Check with a qualified electrician or service personnel if the grounding instructions are not completely understood, or if in doubt as to whether the machine is properly grounded.
- Use only 3-wire extension cords that have 3-prong grounding type plugs and matching 3-conductor receptacles that accept the machine's plug.
- Repair or replace damaged or worn cord immediately.
- Grounded, cord-connected machines intended for use on a supply circuit having a nominal rating less than 150 Volts:
- This tool is intended for use on a circuit that has an outlet that looks like the one illustrated in Fig. B. The tool has a grounding plug that looks like the plug illustrated in Fig. B. A temporary adapter, which looks like the adapter illustrated in Fig. C, may be used to connect this plug to a 2-pole receptacle as shown in Fig B if a properly grounded outlet is not available. The temporary adapter should be used only until a properly grounded outlet can be installed by a qualified electrician. The green-colored rigid ear, lug, and the like, extending from the adapter must be connected to a permanent ground such as a properly grounded outlet box.
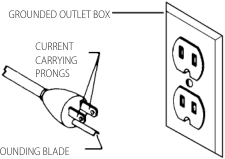
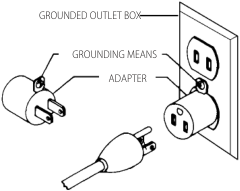
EXTENSION CORDS
Minimum Gauge for Cord Sets
Minimum Gauge for Cord Sets shows the correct gauge to use depending on the cord length. If in doubt, use the next heavier gauge. The smaller the gauge number, the heavier the cord.
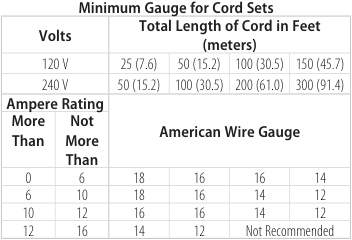
Specifications
- Input: 120V AC, 15 Amp
- No-load speed: 10000 RPM
- Feed speed: 14” (4.3 m) or 26” (7.9 m) per minute
- Planing width: Maximum 6” (152.4 mm)
- Planing depth: Maximum 1/8” (3.2 mm)
- Planing height: Maximum 13” (325 mm)
Electrical Connection
Be sure your power supply agrees with the nameplate marking. Volts, 50/60 Hz or "AC only" means your planer must be operated only with alternating current and never with direct current. Voltage decrease of more than 10% will cause the loss of power and overheating.
Intended Use
This planer is designed for professional wood working.
- DO NOT use under wet conditions or in the presence of flammable liquids or gases.
- DO NOT let children come into contact with the tool. Supervision is required when inexperienced operators use this tool.
Fan-Assisted Chip Ejection System
Your planer is equipped with a fan-assisted chip ejection system to aid in exhausting chips from the unit.
NOTE: It is not recommended that a shop vac be connected to the DW735. The capacity of most vacs does not support the volume of chips ejected during planing. The vacuum hose may clog. It is recommended to use the dust collection system to clean debris from the interior of the tool.
Automatic Carriage Lock
There is no manual carriage lock on your planer. A device that automatically minimizes the movement that causes snipe during planing is designed into the four threaded posts.
Assembly and Adjustments
7
). Serious injury could result.
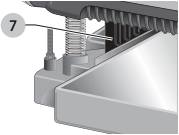
Transporting the Planer (Fig. A)
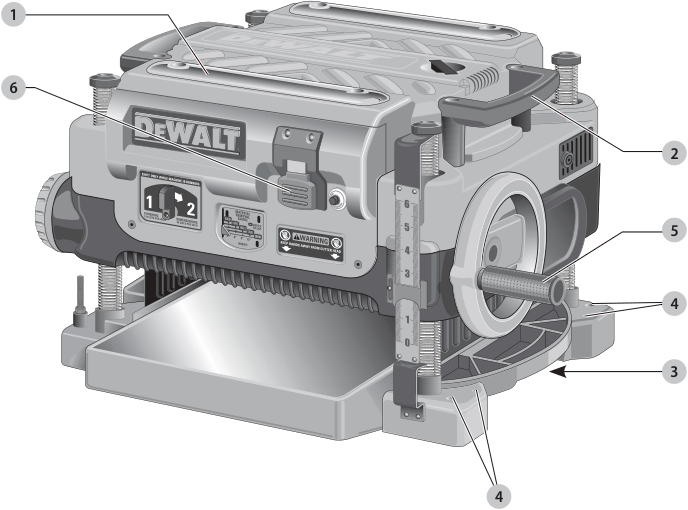
When moving your planer, carry it either by the side carrying handles ( 2
) or by the handles ( 3
) at the base of the planer.
Bench Mounting (Fig. A)
To facilitate bench mounting, two different sized holes ( 4
) are provided on the four corners of your planer. If mounting the planer with bolts, use the larger holes. If mounting the planer with nails or screws, use the smaller holes. It is not necessary to use both sets of holes.
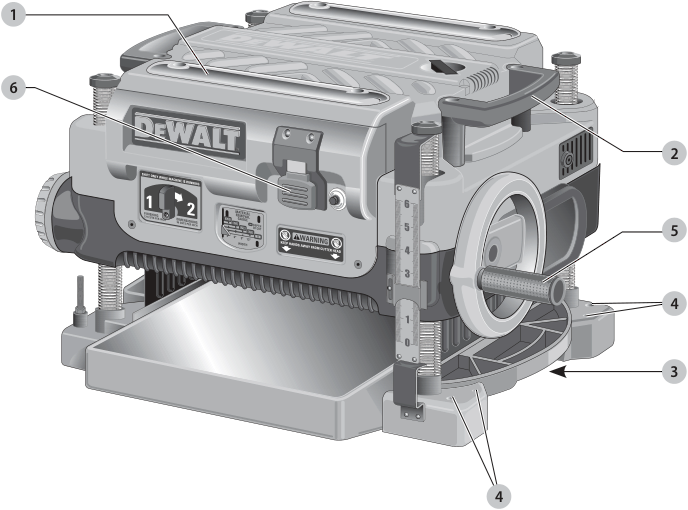
Always mount your planer firmly to prevent movement. To enhance the tool’s portability, it can be mounted to a piece of 1/2” (12.7 mm) or thicker plywood which can then be clamped to your work support or moved to other job sites and reclamped.
To Attach the Depth Adjustment Crank Handle (Fig. E)
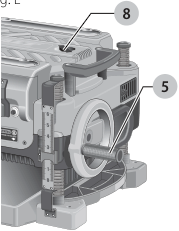
- Remove the screw located in the crank handle shaft.
- Insert the crank handle (
5
) over the shaft. - Secure in place with the screw and T-wrench (
8
) provided.
Dust Ejection Ports (Fig. F)
Your planer comes with a dust ejection port. The round port as shown in Figure F is for use with a 4” (100 mm) dust collector hose.
To Set Up Dust Ejection (Fig. F)
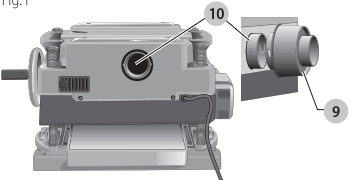
- Select the port (
9
). - Depress the lock button (
11
) on the chip ejection chute (10
). - Slide the notches in the dust port over the pins on the chip ejection chute.
- Rotate the port until the button engages the dust ejection chute and locks in place.
To Remove the Dust Ejection Port (Fig. F)
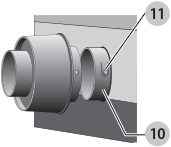
- Use the T-wrench to depress the lock button on the dust chute.
- Twist the port until the pins are disengaged from the notches on the port.
- Pull the dust ejection port off of the dust chute.
Depth Adjustment (Fig. G)
Depth Adjustment Scale (Fig. G)
The depth adjustment scale, located on the right front of your planer, indicates the finished thickness of your workpiece. One rotation of the depth adjustment crank is equal to 1/16” (1.6 mm), half rotation is equal to 1/32” (0.8 mm), etc.
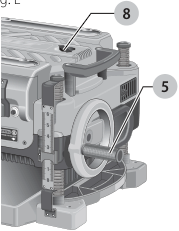
Depth Adjustment Crank
Turning the crank clockwise lowers the cutterhead. Turning the crank counterclockwise raises the cutterhead.
Turret Stop (Fig. H)
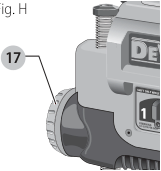
Your planer is equipped with a turret stop for planing multiple boards to the same pre-set depth. Stops are set at 1/8" (3 mm), 1/4" (6.5 mm), 1/2" (12.7 mm), 3/4" (19 mm), 1" (25.5 mm), and 1-1/4" (32 mm).
To Set the Minimum Depth to Which the Carriage can Travel with the Turret Stop
- Be sure the carriage is set above 1-1/4” (32 mm) before trying to set the turret stop.
- Turn the dial on the front left of the planer until the desired thickness setting aligns with the red indicator, then lower the carriage.
- Plane the workpiece at desired increments until the correct final thickness is achieved.
OPERATION
On/Off Switch (Fig. I)
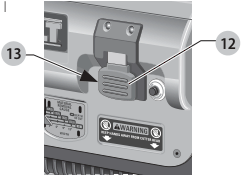
To turn the planer on, lift the switch up. The planer locks on automatically. To turn the tool off, press the switch down. A hole is provided under the switch for insertion of a padlock to lock off the planer.
Speed Selection (Fig. J)
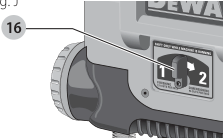
Your planer has the ability to feed material at two different speeds. The two-speed feature was designed to improve efficiency when planing and to provide the best possible surface finish to a variety of materials.
To remove material thickness more quickly, set the unit at speed “2”. This setting delivers 96 cuts per inch to the material. For finishing, set the unit to speed “1”. Speed “1” is ideal for ensuring the finest finish on the last pass before your final thickness is achieved.
Material Removal Gauge (Fig. K)
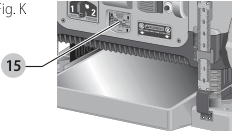
Your planer is equipped with a material removal gauge. It is used to indicate the amount of wood that will be removed in one pass with the carriage set at its current height.
To Use the Material Removal Gauge
- Slide approximately 3" (75 mm) of your material under the middle of the carriage.
- Be sure the wood is lying flat against the base of the planer. If the material is inserted at an angle, the reading may be inaccurate.
- Crank the carriage down on the material until the material removal bar engages the wood. You will see the red arrow begin to move up the scale indicating the amount of material to be removed with the carriage at that height.
- Adjust the carriage height until the desired depth of cut appears on the gauge.
- Pull the material out from under the carriage.
- Turn the unit on and feed your material into the cutterhead.
Planing Basics
Proper Planing Technique
To Plane Your Material
- Lower the carriage to the desired height for your first pass.
- Turn the unit on and feed the material into the feed rollers.
- Examine the finished cut and adjust the carriage to the appropriate height for your next pass.
For best results, plane both sides of the workpiece to reach a desired thickness. For example, if you need to remove 1/8" (3 mm) from your workpiece, remove 1/16" (1.6 mm) from each side. This not only allows the workpiece to dry with an even moisture content, it also produces finer cuts.
WARNING:
- Plane only wood that is free from foreign objects, with no loose knots and as few tight knots as possible. Do not plane wood that is severely warped, twisted, knotted or bowed.
- Do not place your body between the rear of the planer and a stationary object while material is feeding. Serious injury could result.
Minimum/Maximum Width/Height/Depth
NOTE: Always plane in the direction of the grain. Support the workpiece adequately at all times. Planing material less than 3/4" (19 mm) wide is not recommended. If you must plane narrow material, group several pieces together and plane them as one wide workpiece whenever possible.
The maximum depth of cut your planer can take in one pass is 1/8" (3 mm) on material less than 6" (152 mm) wide. Never attempt to modify your planer to take a deeper cut. Follow the recommended depth/width of cut guidelines shown in Table A for best results.
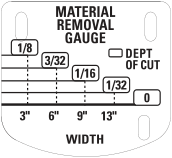
Snipe
Snipe is a depression made when an unsupported end of your material drops toward the floor, causing the opposite end to lift up into the cutterhead.
To Avoid Snipe
- Feed the workpiece into the planer so it is level and remains flat against the base at all times.
- Keep the workpiece level throughout planing operation by receiving or “catching” it from the rear of the planer.
- If you are planing material that is especially long, the use of additional material support is recommended.
Twisted, Cupped and Bowed Wood (Fig. L)
If both sides of your material are very rough or if the material is cupped, bowed, or twisted, your planer may not produce the desired result. Ideally, you should have at least one level face/surface on your material before you plane. Your thickness planer will work best with material that has been run through a jointer to produce one flat surface. If you do not have at least one flat surface or a jointer, see the following recommendations.
To Plane Twisted Wood (Fig. M)
If your material is only slightly twisted:
- Plane both sides alternating from one to the other until the desired thickness is reached.
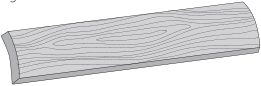
To Plane Cupped Wood (Fig. N)
To obtain the best possible results with cupped wood:
- Rip the material down the middle and plane it as two separate pieces.
Ripping the material reduces the severity of the cup and allows the machine to deliver better results. Understand that you will have to remove more material on cupped wood to achieve the desired thickness than you would on a normal board.
If Ripping the Material is Not an Option
- Plane one side of the material until flat, then plane the opposite side until it is also flat.

To Plane Bowed Wood (Fig. O)
The feed rollers and cutterhead in your planer will push the bow out of the material as it feeds. However, when the material exits the planer, the pressure of the rollers and cutterhead will release allowing the wood to spring back into a bowed formation. To properly remove the bow, use a jointer.
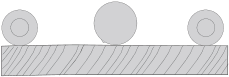
BOWED WOOD WILL BE FLATTENED BY FEED ROLLERS AND CUTTERHEAD...

...BUT BOW WILL RETURN AFTER WOOD IS PLANED
MAINTENANCE
Periodic Maintenance
- Routinely check the tool for damage or broken parts.
- Clean the top cover, dust shroud and all accessible areas of the unit of dust and wood debris that have collected in from planing.
- Wipe off infeed and outfeed rollers.
- Clean base table. Light waxing will help wood material pass through the planer.
- Evaluate blade sharpness condition. Replace as necessary.
- Gauge Calibration, check thickness gauge calibration and turret stop calibration.
- Check brushes for wear and replace as necessary.
Changing or Rotating the Planer Knives
To Change Planer Knives (Fig. P–U)
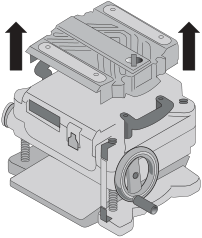
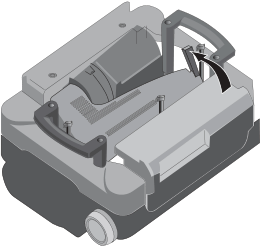
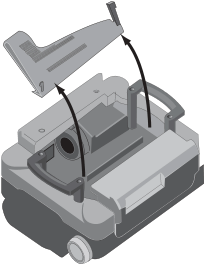
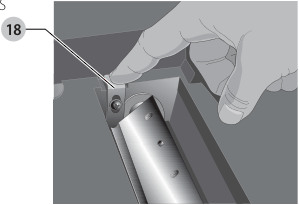
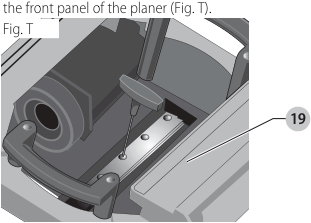
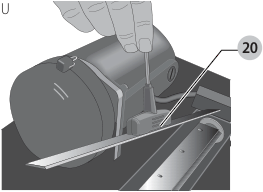
- Use the T-wrench to remove the four screws in the top of the planer.
- Lift the top off (Fig. P) and place it aside.
- Remove the three wing nuts that seal the dust shroud over the cutterhead.
- Rotate the dust shroud up so the round connection that locks onto the fan housing is in the open position (Fig. Q).
- Push the dust shroud to the left so it disengages from the fan housing.
- Take the dust shroud out of the unit (Fig. R) and set it aside.
- The cutterhead is now exposed. If the eight screws in the cutterhead clamp are not visible, use a piece of scrap wood to carefully rotate the cutterhead (Fig. S) until the screws are accessible and the cutterhead lock lever engages. This will prevent further rotation of the cutterhead as you change the knives.
- Use the T-wrench to remove the eight screws on the knife clamp and set them in the small screws bin.
- Use the magnets on the top of the T-wrench to attract the knife clamp and lift it off of the cutterhead. One of the knives should now be exposed.
- Use the magnet to attract the knife. Avoid touching it with your fingers.
If Only One Side of the Knife Is Worn
- Rotate the knife around so that the sharp, unused edge hangs over the end of the cutterhead where it will cut the material. Be sure to set the oblong holes in the knife over the pins machined on the cutterhead.
- Reset the knife clamp over the knife. Be sure to align the beveled edge on the clamp with the sharp, cutting edge of the knife. If these are not aligned correctly, the clamp will not secure the knife properly.
- Install the screws into the clamp and tighten sufficiently.
To Access the Other Two Knives
- Depress the cutterhead lock lever.
- Use the piece of scrap wood to carefully turn the cutterhead until it locks into place, revealing another knife clamp.
- Follow the same knife change procedure indicated above.
- Repeat the procedure for the last dull knife.
After Installing New Knives
- Insert the round end of the dust shroud into the fan housing and rotate it down to lock it into place.
- Place the three wing nuts back into the shroud.
- Screw the top cover of the planer back onto the unit.
Brush Change (Fig. V, W)
Your planer is equipped with brush caps that are external to the motor. If your brushes need to be replaced, begin by acquiring a new set from a DeWALT service center or a dealer authorized to service DeWALT products. Use only identical DeWALT brushes.
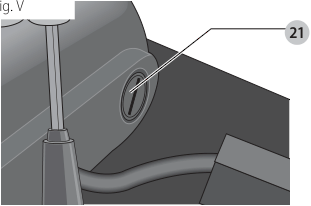
To Replace the Brushes on your Planer (Fig. V, W)
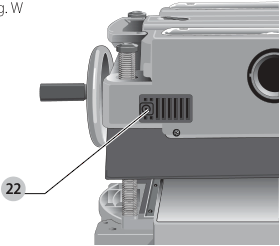
- Use the T-wrench to remove the top cover and brush cover screen on the planer.
- Use a flathead screwdriver to unscrew the brush cap located in the right, rear of the unit.
- Do the same for the brush cap located on the side of the motor, inside the planer cover.
- Place the new brushes into the brush holders.
- After installing the brushes, replace the top cover and brush cover screen.
- Before using the planer, run the unit for 10 minutes to seat new brushes.
Calibrating the Depth Adjustment Scale (Fig. X)
The depth adjustment scale 14 on your planer is set at the factory. However, with extended use, the depth adjustment scale could show an incorrect measurement. To check the depth adjustment scale, plane a piece of scrap wood, noting the measurement on the depth adjustment scale.
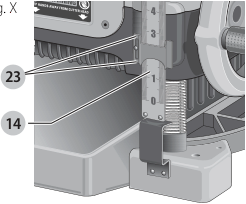
Measure the finished thickness of the workpiece. If the thickness of the workpiece does not match the reading on the depth adjustment scale, loosen the two screws 23 on the red indicator. Adjust the pointer up or down until its reading matches the finished thickness of the workpiece. Securely re-tighten the screws.
Base Maintenance
Keep the table clean and free from oil, grease, and pitch. Treat the table with paste wax to help maintain its smooth finish.
Circuit Breaker Reset Button (Fig. Y)
Your planer is equipped with an 18 amp circuit breaker. If your planer becomes overloaded and stops operating, turn off the planer, let the unit sit for 2 minutes and press the reset button 24 before you resume working.
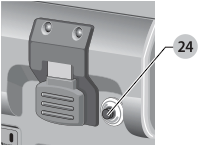
See the Troubleshooting Guide for additional information on circuit breaker trips.
Replacing the Drive Belt
Drive belts are available at extra cost at DeWALT authorized service centers. Replacement of the drive belt should be performed by qualified service personnel.
Chip Ejection Fan (Fig. P–R, Z)
The chip ejection fan on your planer should be cleaned or cleared of debris periodically.
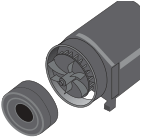
To Access the Fan
- Remove the top cover of the planer with the T-wrench.
- Remove the dust shroud (Fig. P–R) and place it aside.
- Remove the screws and clips around the fan housing.
- Remove the fan housing and place it aside as shown. The fan will now be exposed for cleaning.
See the Troubleshooting Guide for additional information.
Cleaning
It is recommended that, once a year, you take or send the tool to a DeWALT certified service center for a thorough cleaning, inspection and lubrication of the gear case.
Accessories
Recommended accessories for use with your tool are available at extra cost from your local dealer or authorized service center. If you need assistance in locating any accessory, please contact DeWALT Industrial Tool Co., 701 East Joppa Road, Towson, MD 21286, call 1-800-4-DeWALT (1-800-433-9258) or visit our website: www.DeWALT.com .
Four accessories are available for the DW735 Thickness Planer.
- DW7350 Mobile Stand
- DW7351 Folding Tables
- DW7352 13" (325 mm) Knives
- DW7353 Chip Ejection Accessory
DW7351 Accessory Folding Tables (Fig. AA)
Your DW7351 folding table box should include:
- 2 folding tables
- 4 nuts
- 4 cap screws
- 4 stepped bolts
- 4 springs
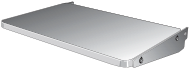
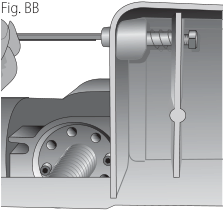
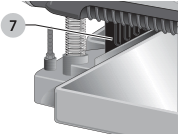
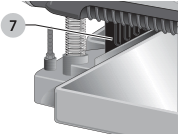
Set-up and Installation of Base Hardware (Fig. BB–DD)
- Place planer on a secure table or workbench. Position planer so the front 3–4" (75–100 mm) of the base can be accessed from the underside.
- Secure the rear of the planer to the table/bench with nails or screws to prevent it from tilting or falling from the table.
- WARNING: The planer could tilt or fall from the table if it is not properly secured opposite the end where the folding table is being installed. Serious injury may result.
- Place the spring onto the small end of the stepped bolt.
- Insert the end of the bolt with the spring around it into the larger hole on the side of the base.
- Push the stepped bolt all the way through the hole in the first rib on the underside of the planer. The spring should engage the rib slightly and the threads should show on the right side of the rib.
- On the underside of the planer, use a wrench to hold the nut in place while turning the stepped bolt into it. The 5/32" (4 mm) hex wrench can be used to turn the stepped bolt until it is fully secured (Fig. BB).
- Install the smaller screw into the lower threaded hole on the side of the base. Use the 5/32" (4mm) hex wrench to tighten that fastener securely (Fig. CC).
- Depress the top pin until it is flush with the base and slide the top hole of the table over the pin and release the pin (Fig. CC, DD).
- To attach the table to the rear of the planer, install the bolts and spring following the above procedure. Your tables should now fold up and down on the top screw and rest on the bottom screw while in position for planing.
- NOTE: To transport the planer with the tables, fold them up and carry the unit as recommended by the planer manual.
- WARNING: For your own safety, it is recommended that two people carry this machine or serious injury could result.
To Remove the Tables
- Depress the spring-loaded bolts on the base and slide each end of the table toward you so they disengage the holes in the tables. You may want to use the T-wrench from your planer to push the bolts flush with the base to easily remove the tables.
- Leave the hardware (stepped bolts and small cap screw) in the base until you need to re-attach the tables.
Repairs
Register Online
Thank you for your purchase. Register your product now for:
- WARRANTY SERVICE : Registering your product will help you obtain more efficient warranty service in case there is a problem with your product.
- CONFIRMATION OF OWNERSHIP : In case of an insurance loss, such as fire, flood or theft, your registration of ownership will serve as your proof of purchase.
- FOR YOUR SAFETY : Registering your product will allow us to contact you in the unlikely event a safety notification is required under the Federal Consumer Safety Act.
Register online at www.DeWALT.com/register .
Three Year Limited Warranty
DeWALT will repair, without charge, any defects due to faulty materials or workmanship for three years from the date of purchase. This warranty does not cover part failure due to normal wear or tool abuse. For further detail of warranty coverage and warranty repair information, visit www.DeWALT.com or call 1-800-4-DeWALT (1-800-433-9258). This warranty does not apply to accessories or damage caused where repairs have been made or attempted by others. THIS LIMITED WARRANTY IS GIVEN IN LIEU OF ALL OTHERS, INCLUDING THE IMPLIED WARRANTY OF MERCHANTABILITY AND FITNESS FOR A PARTICULAR PURPOSE, AND EXCLUDES ALL INCIDENTAL OR CONSEQUENTIAL DAMAGES. Some states do not allow limitations on how long an implied warranty lasts or the exclusion or limitation of incidental or consequential damages, so these limitations may not apply to you. This warranty gives you specific legal rights and you may have other rights which vary in certain states or provinces.
In addition to the warranty, DeWALT tools are covered by our:
1 Year Free Service
DeWALT will maintain the tool and replace worn parts caused by normal use, for free, any time during the first year after purchase.
90 Day Money Back Guarantee
If you are not completely satisfied with the performance of your DeWALT Power Tool, Laser, or Nailer for any reason, you can return it within 90 days from the date of purchase with a receipt for a full refund – no questions asked.
Latin America
This warranty does not apply to products sold in Latin America. For products sold in Latin America, see country specific warranty information contained in the packaging, call the local company or see website for warranty information.
Free Warning Label Replacement
If your warning labels become illegible or are missing, call 1-800-4-DeWALT (1-800-433-9258) for a free replacement.
Troubleshooting Guide
Problem | Possible Cause | Possible Solution |
---|---|---|
If the material does not feed properly | Check for dull knives. | Rotate or replace as necessary. Refer to Changing the Planer Knives section. |
Check for excess clogging in the dust shroud. | Refer to Periodic Maintenance and Figures P-R in the Changing or Rotating the Planer Knives section. | |
Check for excess oil/debris/pitch on feed rollers. | Refer to Periodic Maintenance and Cleaning paragraphs under the Maintenance section. | |
Check for excessively twisted, cupped or bowed material. | Refer to Twisted, Cupped and Bowed Wood paragraph in the Basic Planing section. | |
Check for a broken drive belt. | Refer to Replacing the Drive Belt paragraph in the Maintenance section. | |
If the circuit breaker trips repeatedly | Dull knives | Dull knives can cause motor overloading, rotate or replace as necessary. Refer to Changing the Planer Knives section. NOTE : Circuit breaker overload is often the result of dull knives. If the circuit breaker on your planer trips, check the sharpness of your knives before attempting to reset the breaker in order to continue planing. |
The depth of cut is higher. | An overly aggressive cut could cause motor overloading. Refer to the Depth Adjustment paragraph in the Assembly and Adjustments section and Material Removal Gauge paragraph in the Operation section. | |
The feed rate is higher. | Drop feed rate to 14 ft./min. A reduction in feed rate will reduce the load on the motor and prevent breaker trips. | |
If the unit does not run | Check to see if the unit is plugged in. | Ensure unit is plugged into the appropriate outlet, refer to the General Safety Instructions section. |
Check to see if the top cover is properly in place. | Refer to Figure P for proper location. | |
Check to see if the dust shroud is properly in place. | Refer to After Installing New Knives. | |
Check to see if the circuit breaker needs to be reset. | Refer to Circuit Breaker Reset Button paragraph under the Maintenance section. | |
Check to see if the motor brushes are depleted. | Refer to Brushes paragraph under the Maintenance section. | |
If chips do not eject from the rear of the unit | Check for excess clogging in the dust shroud and fan. | Refer to Periodic Maintenance and Chip Ejection Fan paragraphs in the Maintenance section. |
Check to see if the dust shroud is properly in place. | Refer to After Installing New Knives. | |
If the branch (house/shop) circuit breaker trips repeatedly | Even under normal loading conditions, other electrical loads on the same branch circuit may cause the circuit breaker to trip. | Unplug or turn off other devices sharing the circuit with the planer OR use the planer on another branch circuit by itself. |
Dull knives | Dull knives can cause motor overloading, rotate or replace as necessary. Refer to Changing the Planer Knives section. | |
The depth of cut is higher. | An overly aggressive cut could cause motor overloading. Refer to the Depth Adjustment paragraph in the Assembly and Adjustments section and Material Removal Gauge paragraph in the Operation section. | |
The feed rate is higher. | Drop feed rate to 14 ft./min. A reduction in feed rate will reduce the load on the motor and prevent breaker trips. | |