The DeWALT DW705 Manual is an essential guide for users of the 12" Compound Miter Saw. This detailed manual provides comprehensive instructions on assembly, operation, and maintenance, ensuring you can make precise and safe cuts every time. Along with safety guidelines, it offers troubleshooting tips to help you address common issues and maintain the saw's peak performance. Whether you're a professional or a DIY enthusiast, the DeWALT DW705 Manual equips you with all the information needed to maximize the efficiency of your tool.
DeWALT DW705 Instruction Manual
DW705 12" Compound Miter Saw

DeWALT...BUILT JOBSITE TOUGH
DeWALT high performance industrial tools are made for America's toughest industrial and construction demands. The design of every tool in the line - from drills to sanders to grinders - is the result of rigorous use on jobsites and throughout the industry. Each tool is produced with painstaking precision using advanced manufacturing systems and intense quality control. Every tool is checked before it leaves the factory to make sure that it meets your standards for durability, reliability and power.
DeWALT Built Jobsite Tough... WE GUARANTEE IT.
Important Safety Instructions
READ ALL INSTRUCTIONS
Double Insulation
Double insulated tools are constructed throughout with two separate layers of electrical insulation or one double thickness of insulation between you and the tool's electrical system. Tools built with this insulation system are not intended to be grounded. As a result, your tool is equipped with a two-prong plug which permits you to use extension cords without concern for maintaining a ground connection.
Polarized Plugs
Polarized plugs (one blade is wider than the other) are used on equipment to reduce the risk of electric shock. When provided, this plug will fit in the polarized outlet only one way. If the plug does not fit fully in the outlet, reverse the plug. If it still does not fit, contact a qualified electrician to install the proper outlet. Do not change the plug in any way.
Safety Instructions For All Tools
- KEEP GUARD IN PLACE and in working order.
- REMOVE ADJUSTING KEYS AND WRENCHES. Form habit of checking to see that keys and adjusting wrenches are removed from spindle before turning tool on.
- KEEP WORK AREA CLEAN. Cluttered areas and benches invite accidents.
- DON'T USE IN DANGEROUS ENVIRONMENT. Don't use power tools in damp or wet locations, or expose them to rain. Keep work area well lighted.
- KEEP CHILDREN AWAY. All visitors should be kept at a safe distance from the work area.
- MAKE WORKSHOP KID PROOF with padlocks and master switches, or by removing starter keys.
- DON'T FORCE TOOL. It will do the job better and be safer at the rate for which it was designed.
- USE RIGHT TOOL. Don't force the tool or attachment to do a job for which it was not designed.
- WEAR PROPER APPAREL. No loose clothing, gloves, neckties, rings, bracelets, or other jewelry to get caught in moving parts. Nonslip footwear is recommended. Wear protective hair covering to contain long hair.
- ALWAYS WEAR SAFETY GLASSES. Also use face or dust masks if cutting operation is dusty. Everyday eyeglasses have only impact resistant lenses; they are NOT safety glasses.
- SECURE WORK. Use clamps or a vise to hold work when practical. It's safer than using your hand and it frees both hands to operate the tool.
- DON'T OVERREACH. Keep proper footing and balance at all times.
- MAINTAIN TOOLS WITH CARE. Keep tools sharp and clean for best and safest performance. Follow instructions for lubricating and changing accessories.
- DISCONNECT TOOLS before servicing; when changing accessories such as blades, bits, cutters, etc.
- REDUCE THE RISK OF UNINTENTIONAL STARTING. Make sure the switch is in the OFF position before plugging in.
- USE RECOMMENDED ACCESSORIES. Consult the instruction manual for recommended accessories. The use of improper accessories may cause risk of injury to persons.
- NEVER STAND ON TOOL. Serious injury could occur if the tool is tipped or if the cutting tool is unintentionally contacted.
- CHECK DAMAGED PARTS. Before further use of the tool, a guard or other part that is damaged should be carefully checked to determine that it will operate properly and perform its intended function—check for alignment of moving parts, binding of moving parts, breakage of parts, mounting and any other conditions that may affect its operation. A guard or other part that is damaged should be properly repaired or replaced. Do not use the tool if a switch does not turn it on and off.
Additional Safety Rules For Miter Saws
- CAUTION: FAILURE TO HEED THESE WARNINGS MAY RESULT IN PERSONAL INJURY AND SERIOUS DAMAGE TO THE SAW.
- DO - Protect electric supply line with at least a 15 ampere time-delay fuse or a circuit breaker.
- DO - Make certain the blade rotates in the correct direction and that the teeth at the bottom of the blade are pointing to the rear of the miter saw.
- DO - Be sure all clamp handles are tight before starting any operation.
- DO - Be sure all blade and clamp washers are clean and recessed sides of collars are against blade. Tighten arbor screw securely.
- DO - Keep saw blade sharp and properly set.
- DO - Keep motor air slots free of chips and dirt.
- DO - Use blade guards at all times.
- DO - Keep hands out of path of saw blade.
- DO - Shut off power, disconnect cord from power source and wait for saw blade to stop before servicing or adjusting tool.
- DO - Support long work with an outboard tool rest.
- DON'T - Attempt to operate on anything but designated voltage.
- DON'T - Operate unless all clamp handles are tight.
- DON'T - Use blades larger or smaller than those which are recommended.
- DON'T - Wedge anything against fan to hold motor shaft.
- DON'T - Force cutting action. (Stalling or partial stalling of motor can cause major damage. Allow motor to reach full speed before cutting.)
- DON'T - Cut ferrous metals (Those with any iron or steel content) or any masonry.
- DON'T - Use abrasive wheels. The excessive heat and abrasive particles generated by them will damage the saw.
- DON'T - Allow anyone to stand behind saw.
- DON'T - Apply lubricants to the blade when it's running.
- DON'T - Place either hand in the blade area when the saw is connected to the power source.
- DON'T - Use blades rated less than 4800 R.P.M.
- DON'T - Attempt to cut small pieces (6") without clamping.
- DON'T - Operate saw without guards in place.
- DON'T - Perform any operation freehand.
- DON'T - Reach around or behind saw blade.
- DON'T - Place hands closer than 6 inches from the saw blade.
- DO NOT - Reach underneath the saw unless it is turned off and unplugged. The saw blade is exposed on the underside of the saw.
- DO NOT - Move either hand from saw or workpiece or raise arm until blade has stopped.
- DO NOT - Use without Kerf Plate or when kerf slot is wider than 3/8".
For your convenience and safety, the following warning labels are on your miter saw.
ON MOTOR HOUSING:
- WHEN SERVICING, USE ONLY IDENTICAL REPLACEMENT PARTS.
- ALWAYS WEAR EYE PROTECTION.
ON MOVING FENCE:
- ALWAYS ADJUST FENCE PROPERLY BEFORE USE. CLAMP SMALL PIECES BEFORE CUTTING. SEE MANUAL.
ON GUARD:
- DANGER – KEEP AWAY FROM BLADE.
ON TABLE: (2 PLACES)
- ALWAYS TIGHTEN ADJUSTMENT KNOBS BEFORE USE. KEEP HANDS 6" FROM PATH OF SAW BLADE. NEVER PERFORM ANY OPERATION FREEHAND. NEVER CROSS ARMS IN FRONT OF BLADE. THINK! YOU CAN PREVENT ACCIDENTS.
- DO NOT OPERATE SAW WITHOUT GUARDS IN PLACE. NEVER REACH IN BACK OF SAW BLADE. ALWAYS WEAR EYE PROTECTION. SHUT OFF POWER AND WAIT FOR BLADE TO STOP BEFORE SERVICING, ADJUSTING TOOL, OR MOVING HANDS.
Electrical Connection
Be sure your power supply agrees with the nameplate marking. 120 volts, AC/DC means that your saw will operate on alternating or direct current. A voltage decrease of 10 percent or more will cause a loss of power and overheating. All DEWALT tools are factory tested. If this tool does not operate, check the power supply.
Unpacking Your Saw
Check the contents of your miter saw carton to make sure that you have received all parts. In addition to this instruction manual, the carton should contain:
- One No. DW705 miter saw.
- One No. 340285-01 32 tooth DEWALT 12" dia. saw blade
- One blade wrench in wrench pocket shown in Fig. 2.
Familiarization
Your miter saw is fully assembled (except for the blade) in the carton. Open the box and lift the saw out by the convenient carrying handle, as shown in Figure 1.
Place the saw on a smooth, flat surface such as a workbench or strong table.
Examine Figures 2 & 3 to become familiar with the saw and its various parts. The following section on adjustments will refer to these terms and you must know what and where the parts are.
Press down lightly on the operating handle and pull out the lock down pin, as shown in Figure 4. Gently release the downward pressure and allow the arm to rise to its full height. Use the lock down pin when carrying the saw from one place to another. Always use the carrying handle to transport the saw or the hand indentations shown in Fig. 3.
Specifications
CAPACITY OF CUT
- 48 degree miter left and right
- 48 degree bevel left: 3 degree right
Degree Miter | Max. Height | Result Width | Result Height |
---|---|---|---|
0 degree | Max. Height 3.9" | Max. Width 5.9" | Result Height 2.5" |
45 degree miter | Max. Height 3.9" | Max. Width 4.1" | Result Height 2.5" |
45 degree bevel | Max. Height 2.7" | Max. Width 5.9" | Result Height 1.7" |
DRIVE
- 2000 watts out 13 amp motor
- Cut helical gears with ball bearings
- 32 Tooth carbide blade, 4000 RPM
- Automatic electric brake
Optional Accessories
Extension, Work Support: DW7050
Used to support long overhanging workpieces, the work support is user assembled and stores conveniently under the saw table. Your saw table is designed to accept two work supports; one on each side.
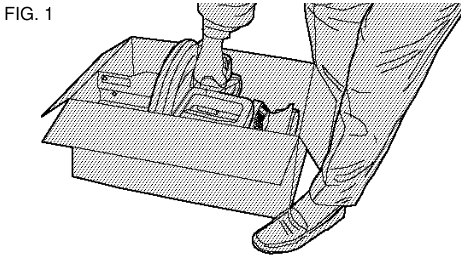
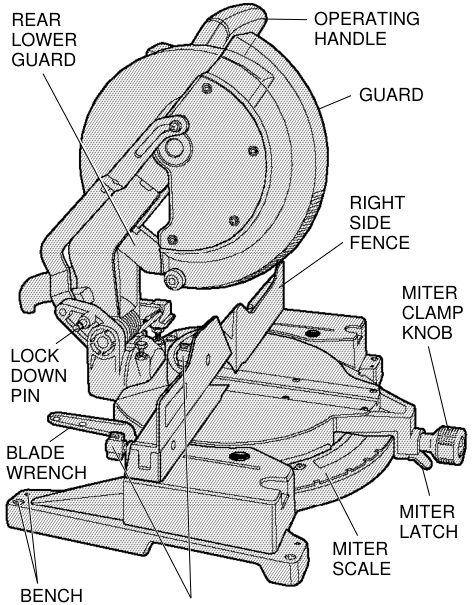
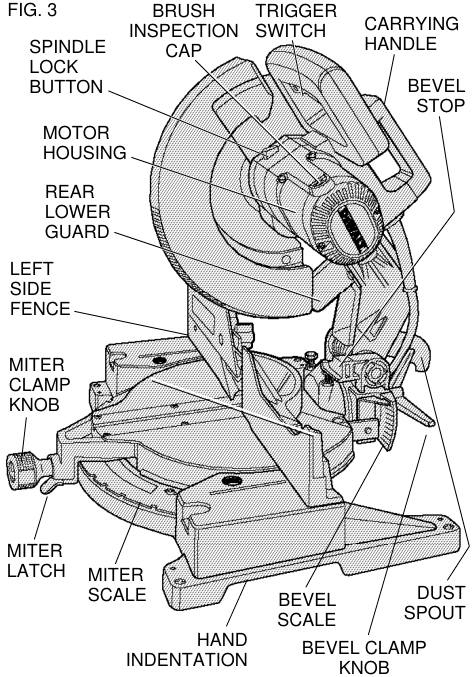
Adjustable Length Stop: DW7051
Requires the use of one work support (see above). It is used to make repetitive cuts of the same length from 0 to 42".
Clamp: DW7052
Used for firmly clamping workpiece to the saw fence for precision cutting
Dust Bag: DW7053
Equipped with a zipper for easy emptying, the dust bag will capture the majority of the sawdust produced. NOTE: Deflector on dust spout channels debris to ground. Spout has a provision to attach a vacuum hose to collect sawdust. Lift dust spout to connect hose.
Crown Molding Fence: DW7054
Used for precision cutting of crown molding.
Kit Box: DW7056
Used to store and transport DW705 accessories.
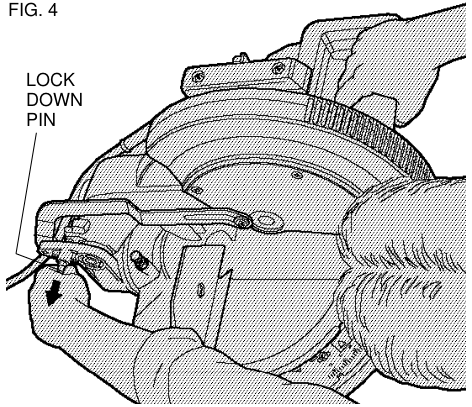
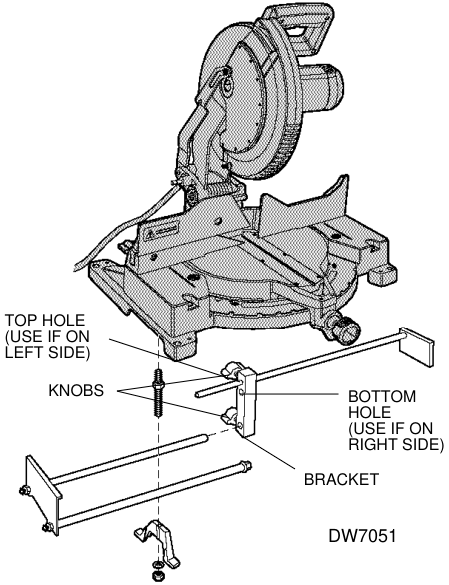
Accessories
Recommended accessories for use with your tool are available at extra cost from your local service center.
If you need assistance in locating any accessory, please contact DEWALT Industrial Tool Company, P.O. Box 158, 626 Hanover Pike, Hampstead, MD 21074 or call 1-800-4-DEWALT (1-800-433-9258).
Bench Mounting
Holes are provided in all four feet to facilitate bench mounting, as shown in Figure 2. (Two different sized holes are provided to accommodate different sizes of screws. Use either hole, it is not necessary to use both.) Always mount your saw firmly to prevent movement. To enhance the tool's portability, it can be mounted to a piece of 1/2" or thicker plywood which can then be clamped to your work support or moved to other job sites and remounted.
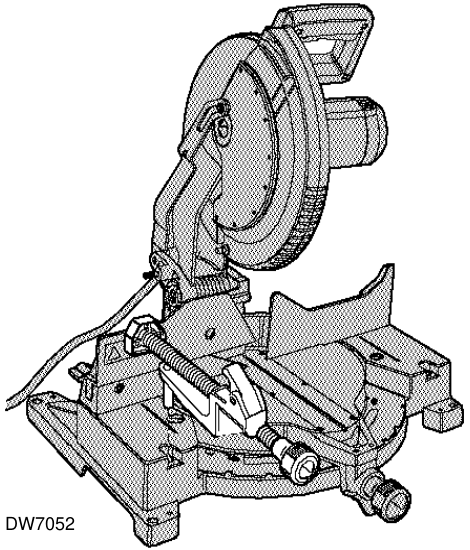
Installing a New Saw Blade
(UNPLUG THE MITER SAW)
DO NOT CUT FERROUS METAL (THAT WITH AN IRON OR STEEL CONTENT) OR MASONRY WITH THIS MITER SAW.
Raise the lower guard as far as possible. Loosen (but do not remove) The guard bracket screw, shown in Figure 5 until the guard bracket can be raised enough to permit access to the blade screw. Hold the lower guard up and depress the spindle lock button with one hand and use the supplied blade wrench in the other hand to loosen (clockwise) the left handed blade screw.
Using the spindle lock, depress the button as shown and rotate the blade by hand until you feel the lock engage. Continue to hold the lock button in to keep the spindle from turning. Remove the blade screw and the blade.
As shown in Figure 6 the inner clamp washer is installed first, then the blade adapter. The blade adapter is designed to permit the use of saw blades with 1" arbor holes as well as blades with 5/8" arbor holes.
When using blades with 1" arbor holes, install the blade adapter over the spindle shaft and against the inner clamp washer, as shown in the figure. Next, install the saw blade making sure that the arbor hole in the blade fits on the blade adapter. Make sure that the teeth at the bottom of the blade are pointing toward the back of the saw (away from the operator). Install the outer clamp washer and install the blade screw. Tighten firmly using the spindle lock and the provided wrench (left hand threads). When using saw blades with 5/8" arbor holes, remove the blade adapter! Save it in a safe place for future use. The rest of the blade assembly is exactly the same. NEVER DEPRESS THE SPINDLE LOCK PIN WHILE THE BLADE IS ROTATING. BE SURE TO HOLD THE GUARD BRACKET DOWN AND FIRMLY TIGHTEN THE GUARD BRACKET SCREW WHEN YOU FINISH INSTALLING THE SAW BLADE. FAILURE TO DO SO WILL CAUSE SERIOUS DAMAGE TO THE SAW.
Rear Lower Guard Adjustment
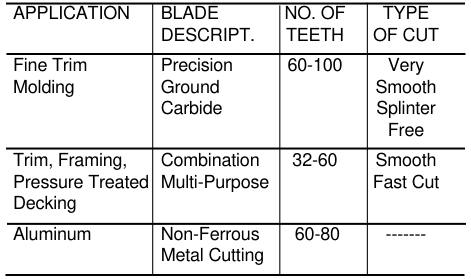
Saw Blades
Part Number | Blade Description | No. Of Teeth | Type of Cut |
---|---|---|---|
Fine Trim Molding | Precision Ground Carbide | 60-100 | Very Smooth Spline Free |
Trim, Framing, Pressure Treated Decking | Combination Multi-Purpose | 32-60 | Smooth Fast Cut |
Aluminum | Non-Ferrous Metal Cutting | 60-80 | ------ |
Cutting the Kerf
In order to adjust and use your miter saw, you must cut a slot through the kerf plate to allow for blade clearance. To cut the kerf plate, set the saw at 0 degrees miter. Place a piece of scrap wood on the saw at least 1"×6"×12". Turn the saw on and allow the blade to reach full speed. Pull the saw arm down as far as it will go and CUT SLOWLY THROUGH THE SCRAP WOOD AND THE YELLOW PLASTIC KERF PLATE. Turn the saw off and allow the blade to stop before raising the saw arm.
Loosen and move the left side of the fence as far as it will go to the left. Now adjust the bevel angle to 45 degrees. Once again, turn on the saw and allow the blade to reach full speed. Pull the arm down and cut slowly through the wood and kerf plate again. (This procedure will widen the kerf plate cut so that the blade will pass through it at any angle from 0 to 45 degrees.)
Be sure to adjust the left side of the fence (see page 8 "Fence Adjustment") so that it's as close to the saw blade as possible without interfering with arm up & down movement. Tighten the fence in position using both knobs.
Transporting the Saw
TURN OFF AND UNPLUG THE MITER SAW BEFORE ATTEMPTING TO MOVE IT OR MAKE ANY ADJUSTMENTS WHAT-SO-EVER!
In order to conveniently carry the miter saw from place to place, a carrying handle has been included on the top of the saw arm, as shown in Figure 3. To transport the saw, lower the arm and depress the lock down pin shown in Figure 4.
Adjustments
Once made, these adjustments should remain accurate. Take a little time now to follow these directions carefully to attain the accuracy of which your saw is capable.
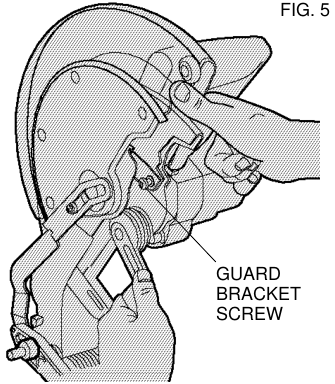
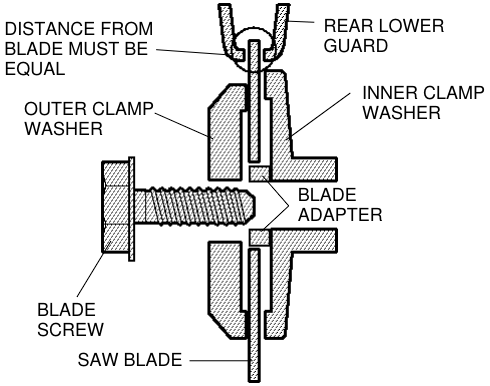
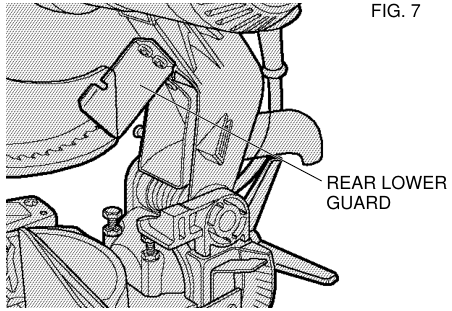
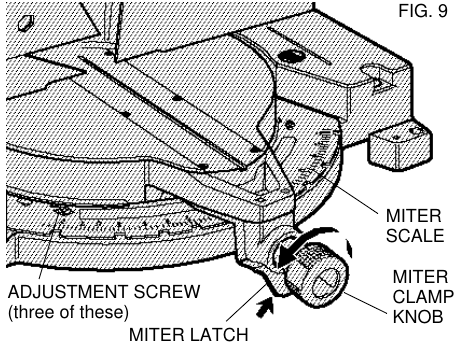
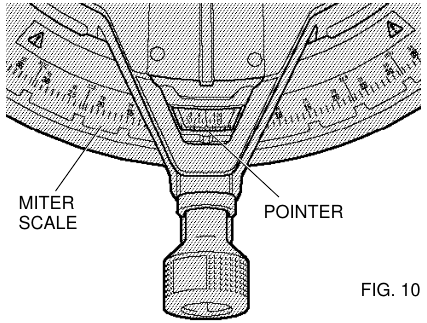
Miter Scale Adjustment
Place a square against the saw’s fence and blade, as shown in Figure 8. Do not touch the tips of the blade teeth with the square. To do so will cause an inaccurate measurement.) Loosen the miter clamp knob (see Fig. 9) and swing the miter arm until the miter latch locks it at the 0 miter position. Do not tighten the clamp knob. If the saw blade is not exactly perpendicular to the fence, loosen the three screws that hold the miter scale to the base (shown in Fig. 9) and move the scale/miter arm assembly left or right until the blade is perpendicular to the fence, as measured with the square. Retighten the three screws. Pay no attention to the reading of the miter pointer at this point.
Miter Pointer Adjustment
Loosen the miter clamp knob and squeeze the miter latch to move the miter arm to the zero position, as shown in Figure 9. With the miter clamp knob loose allow the miter latch to snap into place as you rotate the miter arm past zero. Observe the pointer and miter scale through the viewing opening shown in Figure 10. If the pointer does not indicate exactly zero, carefully pry it left or right using a flat bladed screwdriver.
Bevel Stop Adjustment
Place the saw in the full up position. Loosen the right hand lock nut and turn the stop screw counterclockwise, see Figure 11A. Align the notches in the bevel housing and table as shown in Figure 11A. Place the smooth end of a 1/4" (6.3mm) drill bit into the notches to align the two housings together. While the drill bit is in the notches turn the right bevel stop screw counterclockwise until it is firmly in contact with the bevel stop. Remove the drill bit. Hold the stop screw in place while tightening the lock nut.
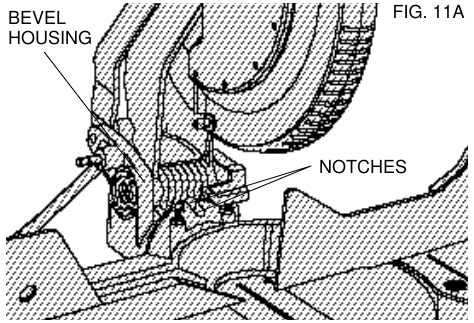
Bevel Pointer
If the bevel pointer does not indicate zero, loosen the screws that hold it in place and move the pointer as necessary.
SUGGESTION: The bevel pointer is quite thick and for accuracy’s sake set the top edge so that it aligns with zero.
Bevel Square to Table
To align the blade square to the rotary table, lock the arm in the down position. Place a square against the blade taking care not to have the square on top of a tooth, as shown in Figure 11B. If the blade is not square, adjust the set screws on the rear of the arm at the pivot pin as shown in Figure 11C. Loosen the bottom screw to move the top of the blade to the right until the blade is aligned to the square. Then tighten the top screw to lock the arm adjustment securely. To move the top of the blade to the left, first loosen the top screw then tighten the bottom screw until the blade is aligned to the square. Be sure the screws have been tightened properly to secure the adjustment against movement.
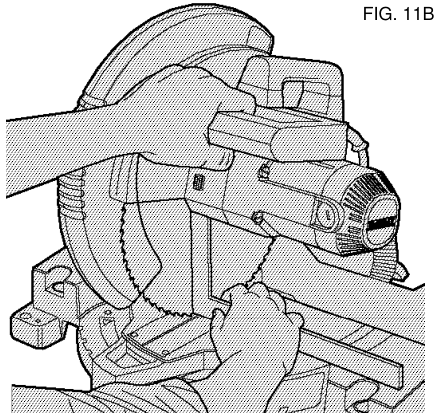
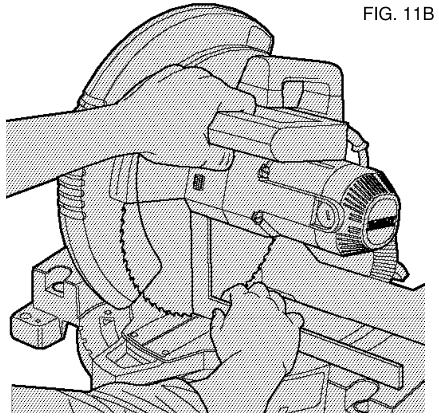
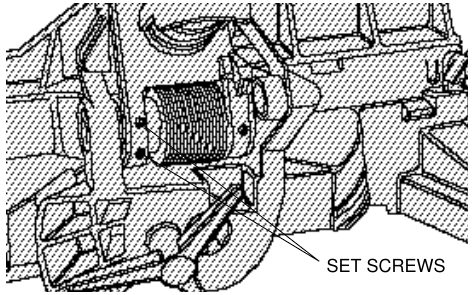
Bevel Stop
To set the 45 degree bevel stop, first loosen the left side fence clamping knobs and slide the left side fence as far as it will go to the left. Move the arm to the left until it stops on the left bevel stop screw. If the bevel pointer does not indicate exactly 45 degrees, loosen the left side bevel stop lock nut and turn the screw downwards. Move the arm to the left and tighten the bevel clamp knob firmly when the bevel pointer indicates exactly 45 degrees. Adjust the left side bevel stop nut upwards until it firmly touches the bevel stop. Retighten the nut while holding the screw firm.
To achieve 3 degree right bevel or 48 degree left bevel, the stop screws must be adjusted to allow the arm to move to the desired position. The bevel stops will need readjustment to the zero and 45 degree positions after this operation.
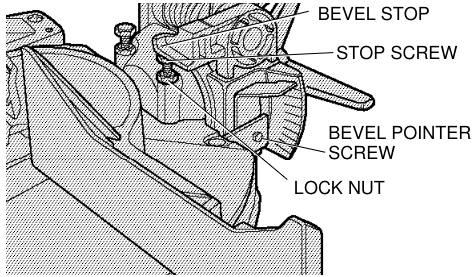
Fence Adjustment
Turn On and Unplug Saw
In order that the saw can bevel to a full 48 degrees left, the left side fence can be adjusted to the left to provide clearance. To adjust the fence, loosen the two fence clamping knobs Figure 13 and slide the fence to the left. Make a dry run with the saw turned off and check for clearance. Adjust the fence to be as close to the blade as practical to provide maximum workpiece support, without interfering with arm up & down movement. Tighten knobs securely. When the bevel operations are complete, don't forget to relocate the fence to the right.
NOTE: The guide groove, shown in Figure 14, of the left side fence can become clogged with sawdust. If you notice that it is becoming clogged, use a stick or some low pressure air to clear the guide groove.
Guard Actuation and Visibility
The blade guard on your saw has been designed to automatically raise when the arm is brought down and to lower over the blade when the arm is raised.
The guard can be raised by hand when installing or removing saw blades or for inspection of the saw. NEVER RAISE THE BLADE GUARD MANUALLY UNLESS THE SAW IS TURNED OFF.
NOTE: Certain special cuts will require that you manually raise the guard.
The front section of the guard is lowered for visibility while cutting. Although the louvers dramatically reduce flying debris, they are openings in the guard and safety glasses should be worn at all times when viewing through the louvers.
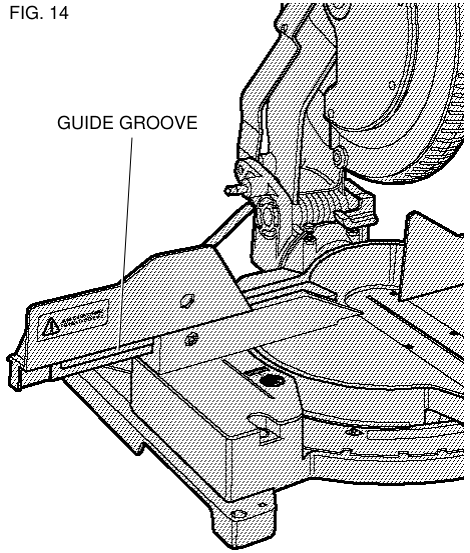
Automatic Electric Brake
Your saw is equipped with an electric blade brake which stops the saw blade within 5 seconds of trigger release. This is automatic and requires no adjustment.
Occasionally, under certain conditions, the brake will not function properly and won’t stop the saw in the 5 seconds as discussed above. If this condition occurs, turn the saw on and off four or five times. If the brake still does not stop the blade in about 5 seconds, the problem may be worn brushes. Replace the brushes as described below and try the saw again. If the problem still persists, have the tool serviced at a Black & Decker service center or company authorized service facility.
Brushes
DISCONNECT PLUG FROM POWER SUPPLY
Inspect carbon brushes regularly by unplugging tool, removing the brush inspection cap (Figure 3) and withdrawing the brush assembly. Keep brushes clean and sliding freely in their guides. Always replace a used brush in the same orientation in the holder as it was prior to its removal. Carbon brushes have varying symbols stamped into their sides, and if the brush is worn down to the line closest to the spring, they must be replaced. Use only identical DEWALT brushes. Use of the correct grade of brush is essential for proper operation of electric brake. New brush assemblies are available at Black & Decker service centers. The tool should be allowed to “run in” (run at no load) for 10 minutes before use to seat new brushes. The electric brake may be erratic in operation until the brushes are properly seated (worn in).
While “running in” DO NOT TIE, TAPE, OR OTHERWISE LOCK THE TRIGGER SWITCH ON. HOLD BY HAND ONLY.
Operation
Plug the saw into any 120 volt 60 Hz power source. Be sure the cord will not interfere with your work.
Switch
To turn the saw on, depress the trigger switch as shown in Figure 15. To turn the tool off, release the switch. There is no provision for locking the switch on, but a hole is provided in the trigger for insertion of a padlock to lock the saw off.
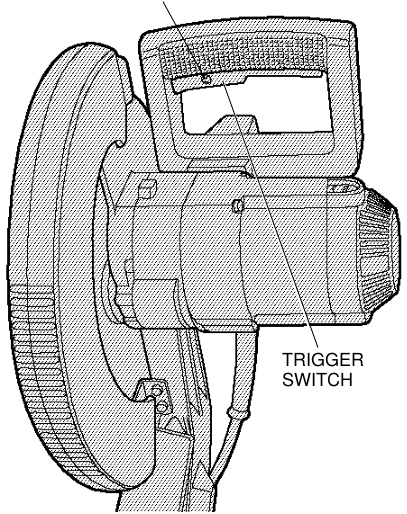
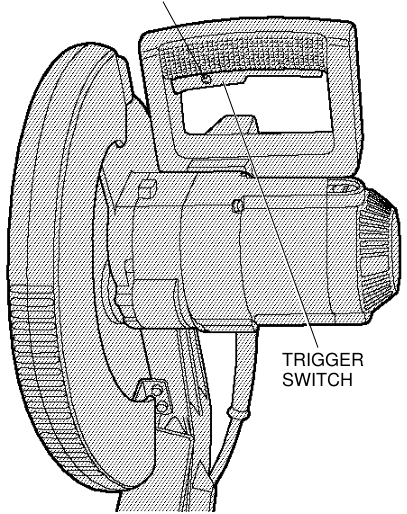
Cutting with Your Saw
NOTE: Although this saw will cut wood and many non-ferrous materials, we will limit our discussion to the cutting of wood only. The same guidelines apply to the other materials. DO NOT CUT FERROUS (IRON AND STEEL) MATERIALS OR MASONRY WITH THIS SAW. Do not use any abrasive blades.
Crosscuts
A crosscut is made by cutting wood across the grain at any angle. A straight crosscut is made with the miter arm at the zero degree position. Set the miter arm at zero, hold the wood on the table and firmly against the fence. Turn on the saw by squeezing the trigger switch as shown in Figure 15.
When the saw comes up to speed (about 1 second) lower the arm smoothly and slowly to cut through the wood. Let the blade come to a full stop before raising arm.
Miter crosscuts are made with the miter arm at some angle other than zero. This angle is often 45 degrees for making corners, but can be set anywhere from zero to 48 degrees left or right. After selecting the desired miter angle, be sure to tighten the miter clamp knob. Make the cut as described above.
Bevel Cuts
A bevel cut is a crosscut made with the saw blade at a bevel to the wood. In order to set the bevel, loosen the bevel clamp knob and move the saw to the left as desired. (It is necessary to move the left side of the fence to allow clearance as you did under “Bevel Stop Adjustment”.) Once the desired bevel angle has been set, tighten the bevel clamp knob firmly.
Bevel angles can be set from 3 degrees right to 48 degrees left and can be cut with the miter arm set between zero and 48 degrees right or left.
Quality of Cut
The smoothness of any cut depends on a number of variables. Things like material being cut, blade type, blade sharpness and rate of cut all contribute to the quality of the cut.
When smoothest cuts are desired for molding and other precision work, a sharp (60 tooth carbide) blade and a slower, even cutting rate will produce the desired results.
Ensure that material does not creep while cutting, clamp it securely in place. Always let the blade come to a full stop before raising arm.
If small fibers of wood still split out at the rear of the workpiece, stick a piece of masking tape on the wood where the cut will be made. Saw through the tape and carefully remove tape when finished.
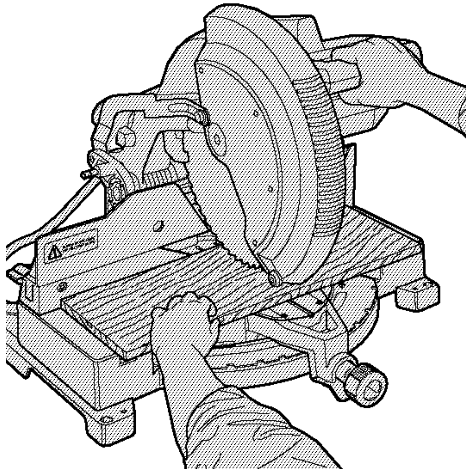
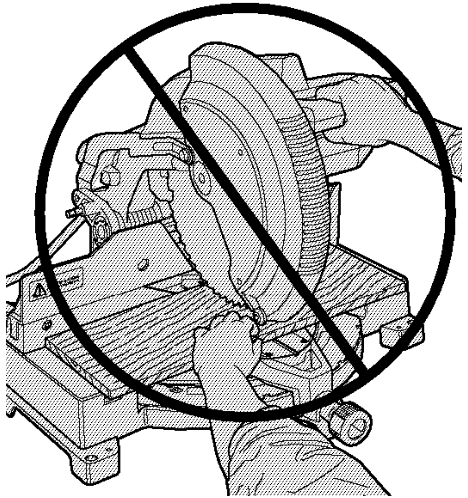
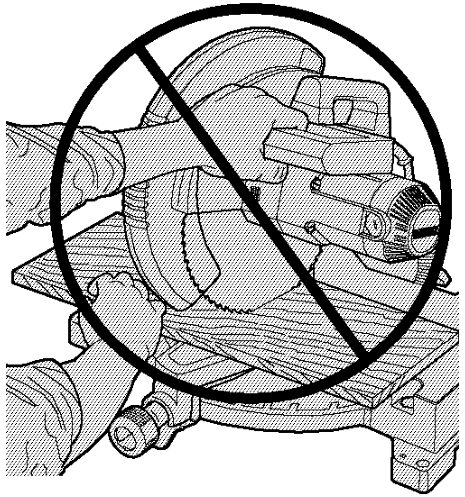
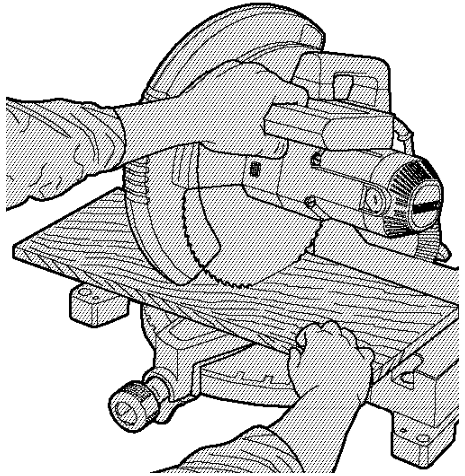
For varied cutting applications
Refer to the list of recommended saw blades for your saw and select the one that best fits your needs.
Body and Hand Position
Proper positioning of your body and hands when operating the miter saw will make cutting easier, more accurate and safer. Never place hands near cutting area. Place hands no closer than 6" from the blade. Hold the workpiece tightly to the table and the fence when cutting. Keep hands in position until the trigger has been released and the blade has completely stopped. ALWAYS MAKE DRY RUNS (UNPOWERED) BEFORE FINISH CUTS SO THAT YOU CAN CHECK THE PATH OF THE BLADE. DO NOT CROSS HANDS, AS SHOWN AT LEFT.
Keep both feet firmly on the floor and maintain proper balance. As you move the miter arm left and right, follow it and stand slightly to the side of the saw blade. Sight through the guard louvers when following a pencil line.
Clamping the Workpiece
Turn Off and Unplug Saw
Always Clamp Wood to the Saw When Possible. You can clamp to either side of the saw blade and remember to position your clamp against a solid, flat surface of the fence. For best results use the DW7052 Clamp made for use with your saw. Available from your dealer at extra cost.
When cutting small pieces requiring your hand to be dangerously close (within 6") to the saw blade, a clamp MUST be used to prevent loss of control. The left fence may be adjusted to aid clamping.
Support for Long Pieces
Turn Off and Unplug Saw
Always Support Long Pieces
For best results, use the DW7050 extension work support to extend the table width of your saw. Available from your dealer at extra cost. Support long workpieces using any convenient means such as saw horses or similar devices to keep the ends from dropping.
Cutting Picture Frames, Shadow Boxes and Other Four Sided Projects
To best understand how to make the items listed here, we suggest that you try a few simple projects using scrap wood until you develop a “FEEL” for your saw.
Your saw is the perfect tool for mitering corners like the one shown in Figure 17. Sketch A in Figure 17 shows a joint made by using the bevel adjustment to bevel the edges of the two boards at 45 degrees each to produce a 90 degree corner. For this joint the miter arm was locked
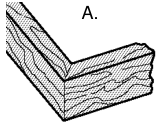
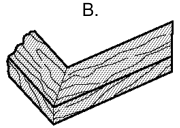
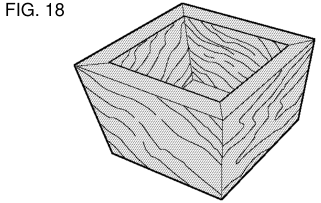
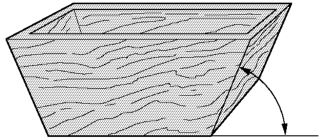
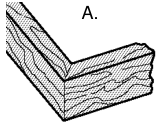
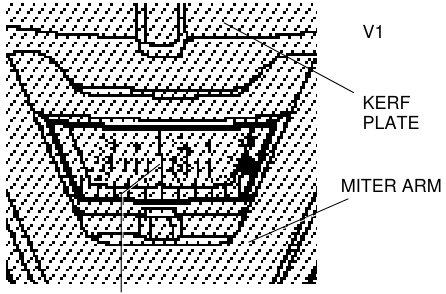
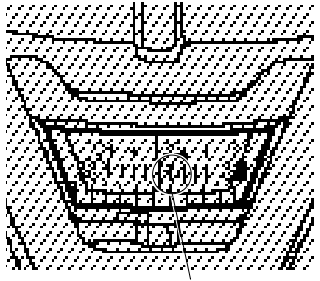
Further Reference Images
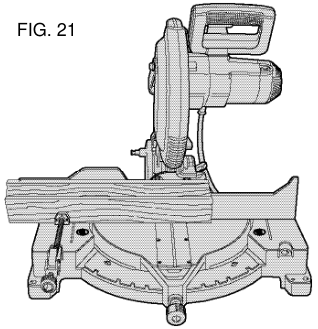
Cutting Compound Miters
A compound miter is a cut made using a miter angle and a bevel angle at the same time. This is the type of cut used to make frames or boxes with slanting sides like the one shown in Figure 18.
NOTE: If the cutting angle varies from cut to cut, check that the bevel angle knob and the miter lock knob are securely tightened. These knobs must be tightened after making any changes in bevel or miter angle.
The chart shown on page 13 will assist you in selecting the proper bevel and miter settings for common compound miter cuts. To use the chart, select the desired angle "A" (Figure 19) of your project and locate that angle on the appropriate arc in the chart. From that point follow the chart straight down to find the correct bevel angle and straight across to find the correct miter angle.
Set your saw to the prescribed angles and make a few trial cuts. Practice fitting the cut pieces together until you develop a feel for this procedure and feel comfortable with it.
Example: To make a 4 sided box with 25 exterior angles (Angle A, Figure 19), use the upper right arc. Find 25 on the arc scale. Follow the horizontal intersecting line to either side to get miter angles setting on saw (23). Likewise, follow the vertical intersecting line to the top or bottom to get the bevel angle setting on the saw (40). Always try cuts on a few scrap pieces of wood to verify settings on saw.
Dual Range Miter Scale
The miter scale has two ranges graduated directly for convenience, as shown in Figure 20. One scale indicates degrees when the blade is square to the fence. At this position the miter scale reads 90 degrees.
Vernier Scale
Your saw is equipped with a vernier scale for added precision. The vernier scale allows you to accurately set miter angles to the nearest 1/4 degree (15 minutes). To use the vernier scale follow the steps listed below.
(As an example, let’s assume that the angle you want to miter is 24 1/4 degrees right).
1. Turn the miter saw.
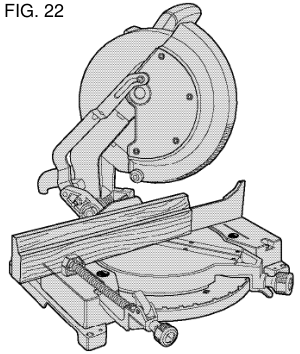
Secure the miter arm lock and carefully move the arm to the RIGHT until the 1/4 degree vernier mark aligns with the CLOSEST degree mark on the miter scale. In our example, the closest degree mark on the miter scale happens to be 35 degrees. Figure V2 shows a setting of 24-1/4 degrees right miter.
On parts that require partial degrees (1/4, 1/2, 3/4 degrees) align the desired vernier mark with the CLOSEST degree mark on the miter scale, as described below (The plastic vernier plate is inscribed with marks for 1/4, 1/2, 3/4 and 1 degrees. Only the 1/2 degree and the 1 degree are numerically labeled).
When Mitering to the Right
Angle the miter angle when mitering to the right, move the arm to align the appropriate vernier mark with the closest mark on the miter scale to the right. To decrease the miter angle when mitering to the right, move the arm to align the appropriate vernier mark with the closest mark on the miter scale to the left.
When Mitering to the Left To increase the miter angle when mitering to the left, move the arm to align the appropriate vernier mark with the closest mark on the miter scale to the left. To decrease the miter angle when mitering to the left, move the arm to align the appropriate vernier mark with the closest mark on the miter scale to the right.
Cutting Base Molding
Always make a dry run without power before making any cuts.
Straight 90 degree cuts —
- Position the wood against the fence and clamp it in place as shown in Figure 21. Turn on the saw, allow the blade to reach full speed and lower the arm slowly through the cut.
Cutting Base Molding Up to 3-7/8" high vertically against the fence
Position the molding as shown in Figure 22.

Cutting Trim Molding and Other Frames
Sketch B in Figure 17 shows a joint made by setting the miter arm at 45 degrees to miter the two boards to form a 90 degree corner. To make this type of joint, set the bevel adjustment to zero and the miter arm to 45 degrees. Once again, position the wood with the broad flat side on the table and the narrow edge against the fence.
The two sketches in Figure 17 are for four side objects only. As the number of sides changes, so do the miter and bevel angles. The chart below gives the proper angles for a variety of shapes.
(The chart assumes that all sides are of equal length). For a shape that is not shown in the chart, use the following formula: 180 degrees divided by the number of sides equals the miter or bevel angle.
Examples
No. Sides | Angle of Miter or Bevel |
---|---|
4 | 45° |
5 | 36° |
6 | 30° |
7 | 25.7° |
8 | 22.5° |
9 | 20° |
10 | 18° |
Cutting 3-7/8" – 5-1/2" Base Molding Vertically Against the Fence
- Position molding as shown in Figure 22.
- All cuts made with the back of the molding against the fence.
Inside Corner:
Left side
- Position molding with bottom of molding against the base of the saw.
- Miter left at 45°
- Save left side of cut
Right side
- Position molding with top of the molding rests on the base of the saw
- Miter left at 45°
- Save left side of cut
Outside Corner:
Left side
- Position molding with bottom of molding against the base of the saw
- Miter right at 45°
- Save left side of cut
Right side
- Position molding with top of the molding resting on the base of the saw.
- Miter left at 45°
- Save right side of cut
Material up to 3.9" (3-7/8") can be cut as described above. For wider boards (up to 5.5" (5-1/2")) several minor concessions must be made.
If you position the base molding vertically against the fence as in Figure 22, the saw can only cut through the board up to 1 inch from the end of the board. Trying to cut more than an inch will cause the saw’s guard case to interfere with the workpiece. If you want to cut base molding between 3-7/8" and 5-1/2" wide vertically follow the directions below.
Cutting 3-7/8"–5-1/2" Base Molding
Vertically Against the Fence
- Position molding as shown in Figure 22
- All cuts made with the back of the molding against the fence.
Inside Corner:
Left side
- Position molding with bottom of molding against the base of the saw.
- Miter left 45°
- Save left side of cut
Right side
- Position molding with top of molding resting on the base of the saw.
- Miter left at 45°
- Save left side of cut
Outside Corner:
Left side
- Position molding with bottom of molding against the base of the saw.
- Miter right at 45°
- Save left side of cut
Right side
- Position molding with top of the molding resting on the base of the saw.
- Miter left at 45°
- Save left side of cut
Cutting Crown Molding
Your miter saw is better suited to the task of cutting crown molding than any tool made. In order to fit properly, crown molding must be compound mitered with extreme accuracy.
The two flat surfaces on a given piece of crown molding that are at angles that, when added together, equal exactly 90 degrees. Most, but not all, crown molding has a top rear angle (the section that fits flat against the ceiling) of 52 degrees and a bottom rear angle (the part that fits flat against the wall) of 38 degrees.
Your miter saw has special pre-set miter latch points at 31.62 degrees left and right for cutting crown molding at the proper angle. There is also a mark on the Bevel scale at 33.85 degrees.
Pretesting with Scrap Material
Instructions for Cutting Crown Molding laying flat and using the compound features
- Molding laying with broad back surface down flat on saw table.
- The settings below are for All Standard (U.S.) crown molding with 52° and 38° angles.
Bevel Setting
When mitering to the right:
Bevel Setting | Type of Cut |
---|---|
33.85° | |
Right Side, Inside Corner: | |
1. Bottom of molding against fence | |
2. Miter table set left 31.62° | |
3. Save left end of cut | |
Right Side, Outside Corner: | |
1. Bottom of molding against fence | |
2. Miter table set left 31.62° | |
3. Save right end of cut | |
When mitering to the left:
Bevel Setting | Type of Cut |
---|---|
33.85° | |
Left Side, Inside Corner: | |
1. Top of molding against fence | |
2. Miter table set right 31.62° | |
3. Save left end of cut | |
Left Side, Outside Corner: | |
1. Top of molding against fence | |
2. Miter table set right 31.62° | |
3. Save right end of cut | |
Always make a dry run WITHOUT power before making any cuts. Practice fitting your pieces together before trimming more expensive molding elements or full rafters.
Table 1 - Compound Miter Cut
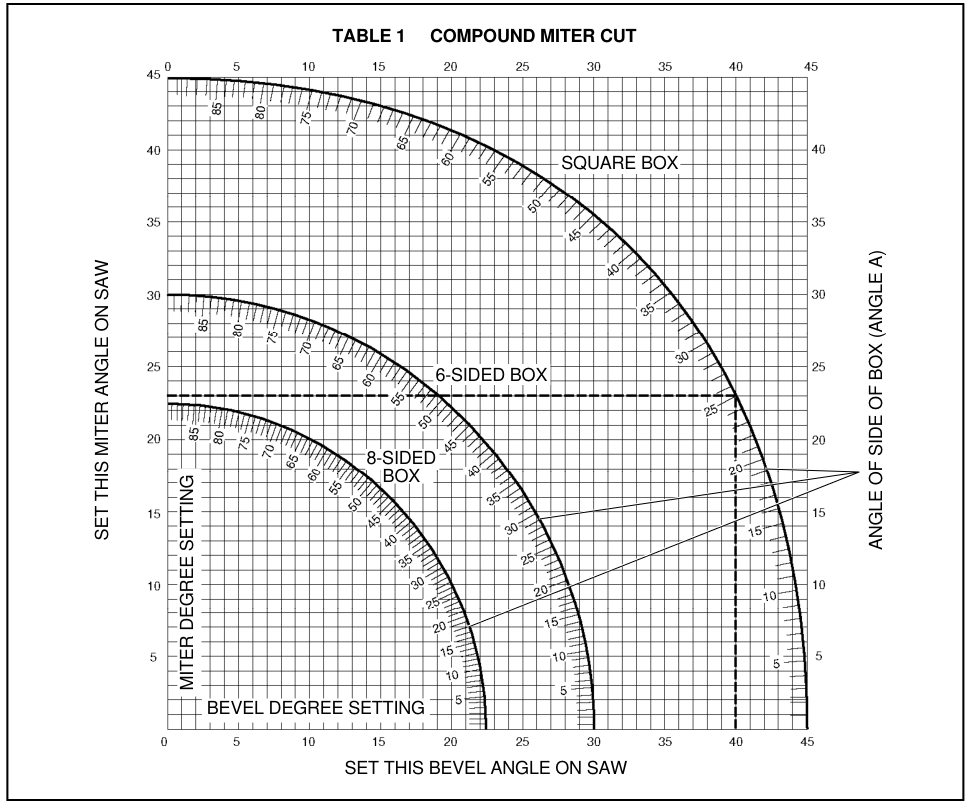
Alternative Method for Cutting Crown Molding
Place the molding on the table at an angle between the fence and the saw table as shown in Figure 26. Use of the crown molding fence accessory (DW7054) is highly recommended because of its degree of accuracy and convenience. The crown molding fence accessory is available at extra cost from your local dealer. The advantage to cutting crown molding using this method is that no bevel cut is required. Minor changes in the miter angle can be made without affecting the bevel angle. This way, when corners other than 90 degrees are encountered, the saw can be quickly and easily adjusted for them. Use the crown molding fence accessory to maintain the angle at which the molding will be on the wall.
Instructions for Cutting Crown Molding Angled Between the Fence and Base of the Saw for All Cuts:
- Angle the molding so the bottom of the molding (part which goes against the wall when installed) is against the fence and the top of the molding is resting on the base of the saw as shown in figure 26a.
- The angled "flats" on the back of the molding must rest squarely on the fence and base of the saw.
Inside Corner:
Left side
- Miter right at 45°
- Save the right side of cut
Right side
- Miter left at 45°
- Save the right side of cut
Outside Corner:
Left side
- Miter left at 45°
- Save the right side of cut
Right side
- Miter right at 45°
- Save the left side of cut
Special Cuts :
Aluminum Cutting Aluminum extrusions such as those used when making aluminum screens and storm windows can easily be cut with your saw. Position the material so that you will be cutting the thinnest cross section as shown in Figure 27. Figure 28 illustrates the wrong way to cut these extrusions. Use a wax lubricant when cutting aluminum such as Johnson’s Stick Wax No. 140. Apply the stick wax directly to the saw blade before cutting. Never apply stick wax to a moving blade.
Maintenance
- All bearings are sealed ball bearings. They are lubricated for life and need no further maintenance.
- Periodically clean all dust and wood chips from around AND UNDER the base and the rotary table. Even though slots are provided to allow debris to pass through, some dust will accumulate.
- The brushes are designed to give you several years of use. If they ever need replacement, follow the instructions on page 8 or return the tool to the nearest service center for repair. Service center locations are packed with your tool.
Troubleshooting Guide
Trouble: Saw will not start What's Wrong?
- Saw not plugged in
- Fuse blown or circuit breaker tripped
- Cord damaged
- Brushes worn out What to Do...
- Plug in saw.
- Replace fuse or reset circuit breaker
- Have cord replaced by authorized service center or replace them yourself as instructed on page 10.
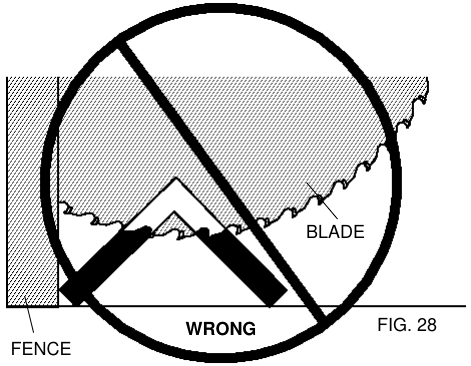
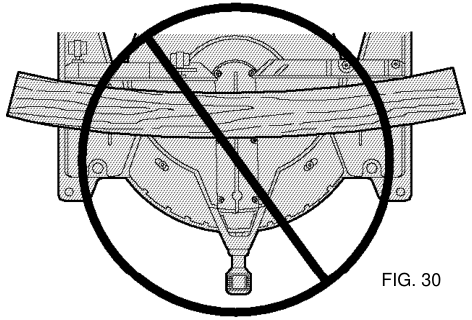
Important
To assure product safety and reliability, repairs, maintenance, and adjustment should be performed by Black & Decker (U.S.) Inc. industrial tool service centers or other qualified service organizations. These service organizations service DeWALT tools always using DeWALT replacement parts.
Full Warranty
DeWALT heavy duty Industrial tools are warranted for one year from date of purchase. We will repair, without charge, any defects due to faulty materials or workmanship. Arrangements have been made with the Industrial Tool Division of Black & Decker (U.S.) Inc. to provide warranty repairs for DeWALT tools. Please return the complete unit, transportation prepaid, to any Black & Decker (U.S.) Inc. industrial service center or authorized service station listed under "Tools, Electric" in the yellow pages. This warranty does not apply to accessories or damage caused where repairs have been made or attempted by others. This warranty gives you specific legal rights and you may have other rights which vary from state to state. 30 DAY NO RISK SATISFACTION GUARANTEE
If you are not completely satisfied with the performance of your DeWALT heavy duty Industrial tool, simply return it to the participating seller within 30 days for a full refund. Please return the complete unit, transportation prepaid. Proof of purchase may be required.